Henderson Conveyor Belt Successfully Swapped Out After 24 Years on the Job
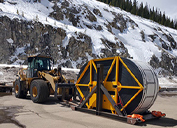
July 5, 2023 - After almost a quarter century on the job, Henderson operations has retired and replaced a piece of the giant magic carpet that delivers its world-class molybdenum ore from mine to mill.
In May, work was completed on the first and largest section of the three conveyor belts that transport moly ore from the Henderson mine near Empire, Colorado, more than 15 miles west across the Continental Divide to the Henderson mill.
“This was an exciting project and a once-in-a-life-of-mine opportunity for the Crush and Convey team to coordinate,” said Jared Youngclaus, Haulage/Crush and Convey Superintendent-Henderson. “A safety-conscious work force, good planning and collaboration helped make this project a huge success.”
The 8,000-foot-long belt weighing more than 300,000 pounds (38 pounds per foot) was brought into the mine in nine reels.
“It’s the first time we’ve changed a primary conveyor belt on the Henderson conveyor system since it was commissioned in 1999, and that belt system has carried more than 150 million tons of ore over that time,” said Henderson Mine Manager Dave Loring. “We hit that milestone in February of this year.”
Advance work critical to change
Six months of prep work was required by electricians, maintenance and Crush and Convey crews to install threadbar anchors, overhead netting, electrical equipment, and portable gantry cranes, move guarding, relocate ventilation duct work, and widen and deepen roads and work areas. This was followed by another five weeks of splicing and setting the new belt adjacent to the old belt.
The plan was completed with pulling the new belt onto the conveyor structure and removing and bringing the old belt up to the surface, which required another couple weeks of work.
“We put so many hours in planning with so many departments involved,” said Crush/Convey Supervisor Chris Tangney. “Every day, we would come up with some little thing to put in the plan that would make the job better or address something that we might have otherwise forgot.”
When it came time to execute the plan, the communication between several different departments and the contractor made for an incident-free install, said Steve Sherman, Crush/Convey Superintendent.
“It went even smoother than we even thought it could, and that was due to the planning and communication,” Sherman said. “That’s a lot of work between departments to get done within a five-day maintenance period.”
The coolest part of the installation process for Youngclaus was watching the contractor splice the belt together.
“It’s a process that’s called ‘faloosing’ that is similar to festooning a ribbon, so they cook the sections of belt rubber together between two plates,” he said.
That said, an even cooler aspect of the vulcanization later came to Youngclaus, he said.
“Ultimately, what was really impressive was that all that planning and prep work allowed us to actually switch out PC1 (Primary Conveyor No. 1) during one of our regular down periods for maintenance, so there was zero negative impact to production to go along with zero incidents,” Youngclaus said. “And this project was of paramount importance to Henderson, because it gives us continued operation until 2038.”
Photos (left to right): The 8,000-foot conveyor belt was assembled from nine reels of material; Contractors “faloose” the new conveyor belt at the Henderson mine.
SOCIAL
RECOGNITION